How to Choose the Best Pallet Racking System for Maximum Warehouse Efficiency
In the ever-evolving landscape of logistics and warehousing, choosing the right Pallet Racking system is crucial for enhancing operational efficiency and maximizing storage capabilities. With the surge in demand for various goods, businesses are increasingly turning to advanced Pallet Racking solutions that not only optimize space but also streamline inventory management.
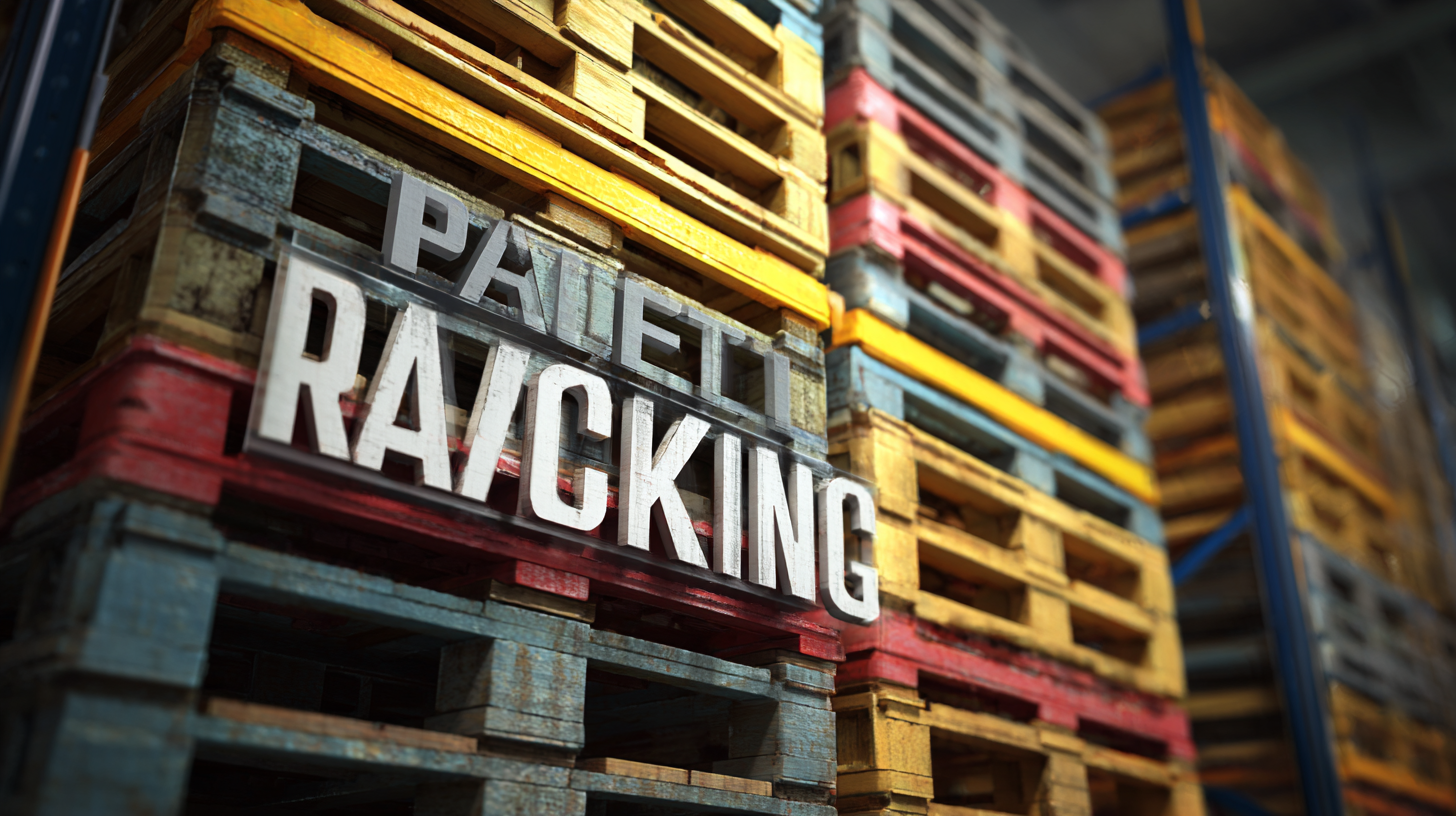
This blog aims to guide you through the essential factors to consider when selecting the best Pallet Racking system tailored to your specific warehouse needs. From understanding the different types of racking available to evaluating their durability and adaptability, we will explore how a thoughtfully chosen Pallet Racking system can significantly impact your warehouse productivity.
As we delve into best practices and considerations, remember that investing in high-quality, reliable Pallet Racking equipment is synonymous with bolstering your warehouse's overall efficiency, ensuring your operations remain competitive in a global market that values quality and performance.
Factors to Consider When Selecting Pallet Racking Systems
When selecting the best pallet racking system for maximizing warehouse efficiency, several key factors should be taken into account. First and foremost, consider the types of goods that will be stored. Different products have varying weight, size, and handling requirements, which influence the design and configuration of the racking system. For instance, heavy and bulky items may require stronger and more robust racks, while smaller products might benefit from more compact solutions. Analyzing your inventory profile can help you determine the most suitable racking type—whether it’s selective, drive-in, or cantilever racking.
Another critical aspect to consider is the warehouse layout and space optimization. Adequate space planning is essential to facilitate smooth operations and ensure safety. Efficient use of vertical space can significantly enhance storage capacity, and racking systems should be designed to allow for easy accessibility and flow of goods. Additionally, as industries increasingly focus on sustainability and energy efficiency, integrating energy storage technologies and sustainable practices into your warehouse operations can further enhance performance. Choosing a racking system that supports your sustainability goals will not only optimize space but also contribute to the overall decarbonization efforts in logistics and distribution.
Evaluating Different Types of Pallet Racking for Your Space
When evaluating different types of pallet racking systems for your warehouse, it is crucial to consider factors such as space utilization, inventory type, and operational efficiency. According to a report by the Warehousing Education and Research Council (WERC), proper pallet racking can lead to up to 50% more efficient use of warehouse space. Two popular racking options are selective racking and drive-in racking.
Selective racking provides easy access to all pallets, making it suitable for warehouses with a diverse range of products. This type of racking is highly adaptable and allows for inventory flexibility, catering to various item sizes and turnover rates.
On the other hand, drive-in racking maximizes storage density by allowing forklifts to drive into the racking systems, significantly reducing aisle space. Research has shown that drive-in racking can increase storage capacity by up to 75% compared to traditional selective systems, making it an optimal choice for facilities with high-volume, low-variability inventories. However, it's essential to assess the specific needs of your operation since drive-in systems may require longer retrieval times. By carefully analyzing these options, you can select a pallet racking system that enhances your warehouse efficiency and supports your business's growth.
Maximizing Warehouse Space: Efficient Layout Strategies
Maximizing warehouse space is crucial for operational efficiency, and efficient layout strategies can significantly enhance productivity. According to a report by the Warehousing Education and Research Council (WERC), optimizing warehouse layout can increase space utilization by up to 30%. This is primarily achieved through strategic placement of pallet racking systems, which not only help in organizing inventory but also reduce travel times for warehouse staff.
One effective layout strategy is the implementation of a flow-through system, which allows for a continuous movement of goods and minimizes congestion. A study by the Material Handling Industry (MHI) indicates that using drive-in and drive-through racking can increase storage density by 100% compared to traditional push-back systems. Additionally, integrating technology such as warehouse management systems (WMS) can enhance inventory accuracy and order picking efficiency, leading to improved overall performance. By thoughtfully designing the warehouse layout, businesses can maximize their square footage and improve operational workflows, leading to greater profitability.
Integrating Technology for Enhanced Racking System Performance
In today's fast-paced logistics environment, integrating technology into pallet racking systems is essential for enhancing warehouse efficiency. A report by the Warehousing Education and Research Council (WERC) indicates that warehouses implementing automated systems can achieve up to a 30% increase in productivity. Utilization of technologies such as RFID, warehouse management systems (WMS), and automated guided vehicles (AGVs) allows warehouse managers to optimize inventory tracking and reduce picking times significantly.
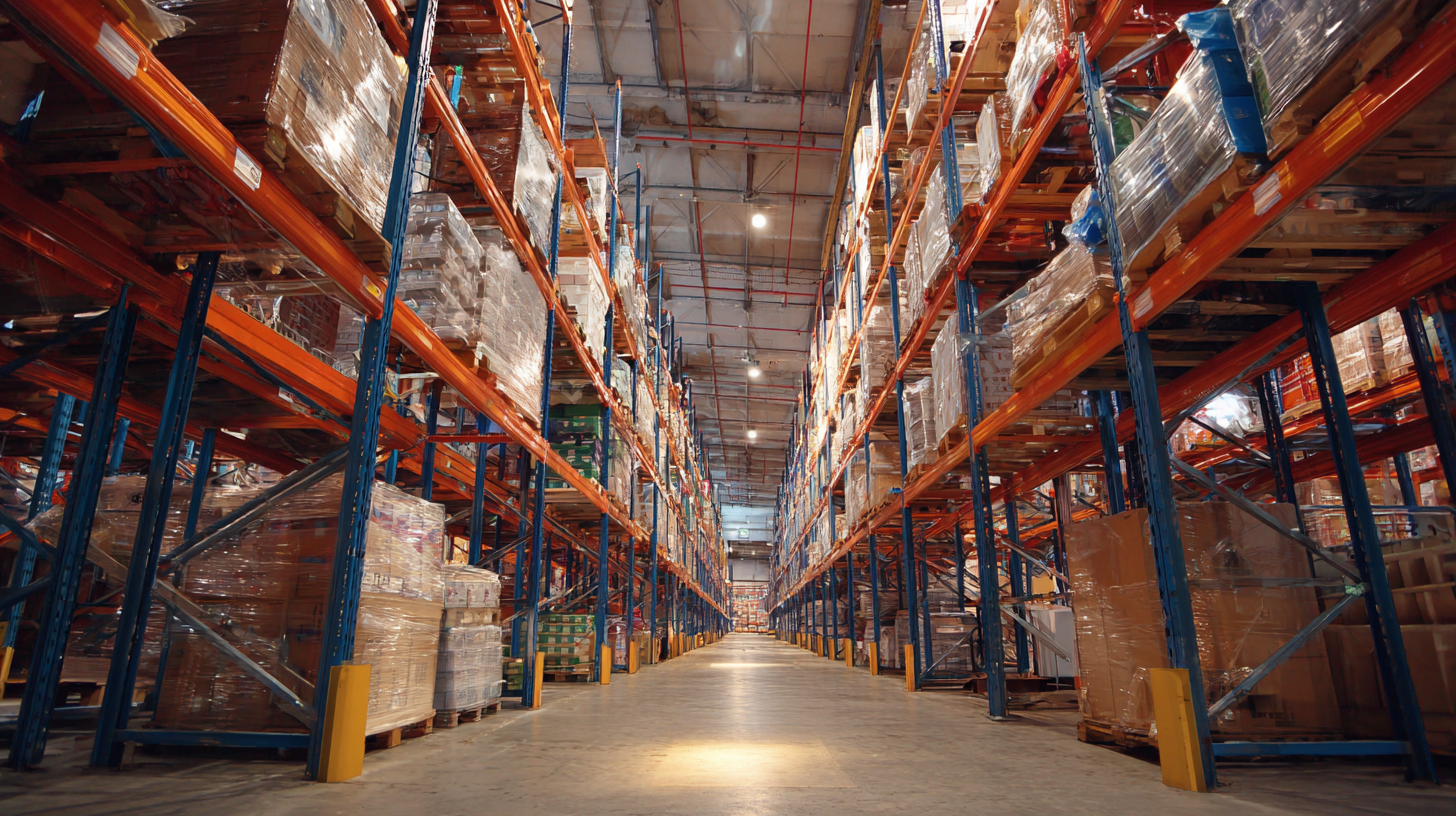
Furthermore, the incorporation of data analytics into racking systems enables real-time monitoring of stock levels and performance metrics. According to a study by Logistics Management, warehouses that leverage data-driven decision-making can see a 25% reduction in operational costs. These technologies facilitate smarter space utilization and improve overall workflow in the warehouse, allowing for better alignment between supply and demand.
By realizing the potential of technological integration, businesses can create a more dynamic and responsive warehouse environment that meets the challenges of modern supply chain demands.
Safety Standards and Compliance in Pallet Racking Solutions
When selecting a pallet racking system, prioritizing safety standards and compliance is crucial. Adhering to regulations such as OSHA and ANSI helps ensure that your warehouse operates within legal parameters and protects your workforce. Compliance not only minimizes the risk of accidents but also enhances the longevity of your racking system. Proper installation, maintenance, and regular inspections are essential to uphold safety standards, allowing you to mitigate hazards associated with load capacities, seismic activity, and aisle width.
Moreover, investing in pallet racking solutions that meet industry safety standards can boost employee morale and promote a safety-conscious culture within your organization. Training staff on the proper use of racking systems, including load checking and safe material handling procedures, further supports compliance efforts. It is also critical to choose racking systems that offer features such as safety clips, upright protectors, and anti-collapse nets, which add an extra layer of protection. By integrating safety as a core component of your racking system selection, you can significantly enhance warehouse efficiency while ensuring a safe working environment for all employees.
How to Choose the Best Pallet Racking System for Maximum Warehouse Efficiency - Safety Standards and Compliance in Pallet Racking Solutions
Pallet Racking Type | Load Capacity (lbs) | Height (ft) | Width (ft) | Depth (ft) | Safety Compliance |
---|---|---|---|---|---|
Selective Racking | 2,500 | 12 | 4 | 3 | ANSI/RMI MH16.1 |
Drive-In Racking | 3,000 | 14 | 6 | 3 | ISO 9001 |
Push Back Racking | 2,200 | 10 | 5 | 4 | S Peek Option |
Cantilever Racking | 4,000 | 15 | 8 | 3 | OSHA Regulations |
Mobile Racking | 2,000 | 12 | 5 | 3 | AFI Standards |